Waterproof and moisture permeable coating agent and its application
Published Time:
2022-11-17
The coating finishing of fabrics is an important branch of textile finishing technology. It can not only endow the fabric with unique style, feel and appearance, but also endow the fabric with various functions and greatly increase the added value of the product.
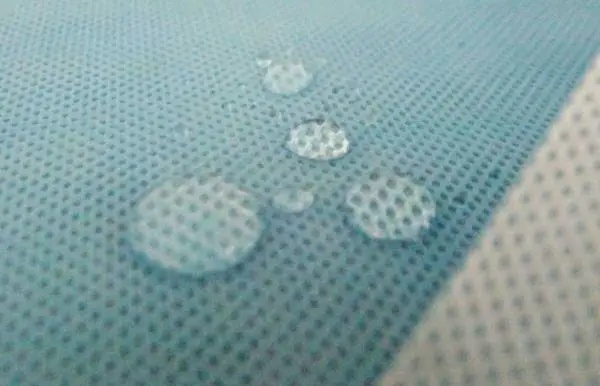
1. Introduction
The coating finishing of fabrics is an important branch of textile finishing technology. It can not only endow the fabric with unique style, feel and appearance, but also endow the fabric with various functions and greatly increase the added value of the product. The main uses of coating products can be divided into three categories: clothing, shoes and hats, industrial cloth and decorative cloth. The consumption of clothing, shoes and hats is the largest. At present, coating products at home and abroad have developed rapidly, and functional coating products such as waterproof and moisture permeable coating, ultraviolet resistant coating, thermal insulation coating, flame retardant coating, shading coating, conductive coating, etc. have emerged. Among them, the waterproof and moisture permeable coating is undoubtedly the most difficult and technical type of functional coating products, which can be widely used in military clothing, sports clothing, special professional clothing, ordinary autumn and winter clothing and footwear cloth.
2. Performance characteristics of waterproof and moisture permeable coating
Waterproof and moisture permeable coating finish can endow the fabric with waterproof, moisture permeable, wind resistant, warm and other functions. It is necessary to maintain a certain temperature and humidity around the human skin, so as to feel comfortable. After wearing clothes, the way of heat dissipation includes radiation, conduction, convection and skin sweat evaporation. Adults sweat about 60~70 ml/h in static state, about 500 ml/d in sports state, and about 1000 ml/h in intense sports state. If sweat can not be released in time, it will not only make the human body feel wet and stuffy due to the increase of moisture on the skin surface, but also lose a lot of heat due to the reason that the heat conduction is much greater in wet environment than in dry environment. The waterproof and moisture permeable fabric can not only resist the penetration of rain, but also resist the invasion of cold wind. It also has the function of automatically adjusting the moisture permeability. It can make the sweat discharged by the human body distribute to the outside of the clothing in time, thus playing the role of moisture permeability and warmth preservation, making the human body feel comfortable.
The diameter of gaseous water molecules is about 0.004um, and the diameter of liquid water molecules is about 100um~6000um. Therefore, the size of micropores in the coating film of the waterproof and moisture permeable coating fabric must be between the two, so that the gas molecules can pass through without the liquid water molecules, so as to achieve the purpose of waterproof and moisture permeability. The permeation process of gaseous water molecules can be completed in two ways. One is that the polar groups and hydrophilic groups in the coating film migrate through the "chemical ladder" action; The second is to make the gaseous water molecules diffuse from the high concentration side to the low concentration side through the amorphous region through the adsorption and desorption of the coating film.
What we call "moisture permeability" is to let water vapor (gaseous water molecules) pass through the fabric. The main factors that determine the waterproof and moisture permeability of the waterproof and moisture permeable coating fabric are:
(1) The microporous structure of the coating film: the microporous size is evenly distributed, and is close to the middle of the gas water molecular diameter and the liquid water molecular diameter (about 0.2um~1.0urn), so the gas water molecule is easy to pass, but the liquid water molecule cannot, which is conducive to the realization of water and moisture permeability.
(2) Molecular structure of the coating film: a certain number of polar groups and hydrophilic groups will improve the moisture permeability.
(3) Strength and thickness of coating film: the coating film with microporous structure has certain tensile strength, and thus has the performance of resisting hydrostatic pressure. The higher the film strength, the stronger the tensile strength, and the stronger the hydrostatic pressure resistance (waterproof ability). The thinner the film thickness is, the worse the tensile strength is, and the worse the hydrostatic pressure resistance is. As the film thickness increases, the tensile strength increases, and its hydrostatic pressure resistance also increases. On the other hand, since moisture permeability is achieved by transferring gaseous water molecules in the film, the thickness of the film also determines the moisture permeability. When the thickness of the coating film increases, the distance to transfer gaseous water molecules increases, the barrier increases, the moisture permeability becomes difficult, and its moisture permeability decreases.
1. Introduction
The coating finishing of fabrics is an important branch of textile finishing technology. It can not only endow the fabric with unique style, feel and appearance, but also endow the fabric with various functions and greatly increase the added value of the product. The main uses of coating products can be divided into three categories: clothing, shoes and hats, industrial cloth and decorative cloth. The consumption of clothing, shoes and hats is the largest. At present, coating products at home and abroad have developed rapidly, and functional coating products such as waterproof and moisture permeable coating, ultraviolet resistant coating, thermal insulation coating, flame retardant coating, shading coating, conductive coating, etc. have emerged. Among them, the waterproof and moisture permeable coating is undoubtedly the most difficult and technical type of functional coating products, which can be widely used in military clothing, sports clothing, special professional clothing, ordinary autumn and winter clothing and footwear cloth.
2. Performance characteristics of waterproof and moisture permeable coating
Waterproof and moisture permeable coating finish can endow the fabric with waterproof, moisture permeable, wind resistant, warm and other functions. It is necessary to maintain a certain temperature and humidity around the human skin, so as to feel comfortable. After wearing clothes, the way of heat dissipation includes radiation, conduction, convection and skin sweat evaporation. Adults sweat about 60~70 ml/h in static state, about 500 ml/d in sports state, and about 1000 ml/h in intense sports state. If sweat can not be released in time, it will not only make the human body feel wet and stuffy due to the increase of moisture on the skin surface, but also lose a lot of heat due to the reason that the heat conduction is much greater in wet environment than in dry environment. The waterproof and moisture permeable fabric can not only resist the penetration of rain, but also resist the invasion of cold wind. It also has the function of automatically adjusting the moisture permeability. It can make the sweat discharged by the human body distribute to the outside of the clothing in time, thus playing the role of moisture permeability and warmth preservation, making the human body feel comfortable.
The diameter of gaseous water molecules is about 0.004um, and the diameter of liquid water molecules is about 100um~6000um. Therefore, the size of micropores in the coating film of the waterproof and moisture permeable coating fabric must be between the two, so that the gas molecules can pass through without the liquid water molecules, so as to achieve the purpose of waterproof and moisture permeability. The permeation process of gaseous water molecules can be completed in two ways. One is that the polar groups and hydrophilic groups in the coating film migrate through the "chemical ladder" action; The second is to make the gaseous water molecules diffuse from the high concentration side to the low concentration side through the amorphous region through the adsorption and desorption of the coating film.
What we call "moisture permeability" is to let water vapor (gaseous water molecules) pass through the fabric. The main factors that determine the waterproof and moisture permeability of the waterproof and moisture permeable coating fabric are:
(1) The microporous structure of the coating film: the microporous size is evenly distributed, and is close to the middle of the gas water molecular diameter and the liquid water molecular diameter (about 0.2um~1.0urn), so the gas water molecule is easy to pass, but the liquid water molecule cannot, which is conducive to the realization of water and moisture permeability.
(2) Molecular structure of the coating film: a certain number of polar groups and hydrophilic groups will improve the moisture permeability.
(3) Strength and thickness of coating film: the coating film with microporous structure has certain tensile strength, and thus has the performance of resisting hydrostatic pressure. The higher the film strength, the stronger the tensile strength, and the stronger the hydrostatic pressure resistance (waterproof ability). The thinner the film thickness is, the worse the tensile strength is, and the worse the hydrostatic pressure resistance is. As the film thickness increases, the tensile strength increases, and its hydrostatic pressure resistance also increases. On the other hand, since moisture permeability is achieved by transferring gaseous water molecules in the film, the thickness of the film also determines the moisture permeability. When the thickness of the coating film increases, the distance to transfer gaseous water molecules increases, the barrier increases, the moisture permeability becomes difficult, and its moisture permeability decreases.
(4) Variety and specification of base cloth: the fabric with flat surface structure, thick thickness and high density has better waterproof ability after coating. The moisture permeability of the fabric before coating also has a great impact on the test of its moisture permeability after coating. Therefore, the evaluation of the moisture permeability of a coating agent should not only look at its moisture permeability after coating, but should compare its moisture permeability before and after coating.
3. Waterproof and moisture permeable coating agent
At present, the coating agents used in textiles are mainly polyacrylate (PA) and polyurethane (PU). PA has a large supply of raw materials and intermediates with low price, and its synthesis and polymerization technology is relatively easy to master. PA coating agent has the advantages of strong adhesion, transparency and non-yellowing, washability, aging resistance, etc., but also has the disadvantages of sticky coating, low water penetration resistance, unpleasant feeling, poor elasticity, poor cold resistance, etc. Its performance can only meet the general requirements, and is not suitable as a waterproof and moisture permeable coating agent. PU coating agent is more unique in performance. It has the advantages of high elasticity, high modulus, low temperature resistance (below - 300C), wear resistance, soft feel, refreshing, and certain hydrophilicity. It is suitable for developing waterproof and moisture permeable coating agent.
PU coating agent is a block polymer composed of two parts of hard segment and soft segment. The hard segment makes PU have strength and elastic modulus, and is composed of various diisocyanates and chain growth agents. Among them, the available diisocyanates mainly include 2,4 and 2,6. toluene diisocyanate (TDI), 4,4-diphenylmethane diisocyanate (MDI), 1,6-hexamethylene diisocyanate (HDI), 3,5,5-trimethyl-2-cyclohexanone diisocyanate (0PDI), and the chain growth agents mainly include diethylenetriamine (DETA) 3, 3 '- dichloro. 4, 4' - diaminodiphenyl methane (MOCA), etc.: The soft segment makes Pu soft and elastic, and is composed of polyols. The size of its molecular weight can also affect the softness and hardness of PU. The choice of polyols is very wide, and polyols with small molecular weight can be used, and polyether or polyester polyol prepolymers with certain molecular weight can also be used.
PU is generally made of diisocyanate, polyether polyol or polyester polyol with chain extender and catalyst through solution polymerization or bulk polymerization. The specific synthesis method shall be determined according to different varieties and requirements. Many properties of PU. Such as glass transition temperature, melting point, modulus, elasticity, tensile strength, water absorption, moisture permeability, etc., can be achieved by changing the type and molecular weight of polyether or polyester glycol prepolymer, the type of diisocyanate, the proportion of hard and soft segments, and the type and amount of chain growth agent.
PU coating agents used in textile industry include solvent type and water dispersion type. The main solvent-based solvents include dimethyl formamide (DMF), butanone, toluene, xylene, isopropanol, ethylene glycol methyl ether, ethylene glycol ether, butanol, ethyl acetate, and their mixtures. The outstanding advantages of solvent type are good film-forming property, water resistance, adhesion and film smoothness, which are better than those of water dispersion type. Also, because the latent heat of solvent vaporization is much less than that of water, the vehicle speed is fast and the production efficiency is high. But its disadvantages are also obvious. For example, most solvents have certain toxicity, volatilize and pollute the environment, and the workshop operating conditions are poor.
Compared with solvent-based coating agent, water-based coating agent has the advantages of clean operation, no environmental pollution, and large changes in performance and style, which is the development direction of PU coating agent.
In terms of waterproof and moisture permeable coating, solvent-based waterproof and moisture permeable coating agent has better film strength, flatness, waterproof performance, washability and other properties than water-dispersed waterproof and moisture permeable coating agent.
Waterproof and moisture permeable coating products can be generally divided into the following three categories: first, products with high moisture permeability and high water pressure, which are generally required to have a moisture permeability of 30009 / (m2d) and a water permeability resistance of 2000mmH2O, which are relatively difficult; Second, the requirement of moisture permeability is high, generally reaching 30009/(m2d), but the requirement of water pressure is not high, such as about 500mmH2O; third, the product with high water pressure requirement and low moisture permeability requirement.
4. Waterproof and moisture permeable coating finishing process
4.1 Coating substrate and pretreatment
In theory. All fabrics can be used as the base cloth for coating finishing, but cotton, hemp, silk, polyester, nylon, viscose and their blended products are mainly used in waterproof and moisture permeable coating finishing. Most types of woven fabrics can be applied to waterproof and moisture permeable coating finishing, such as plain cloth, twill cloth, elastic cloth, oxford cloth, taffeta, satin, straight tribute and other structures. With the continuous innovation and development of coating agent varieties and coating finishing technology, low-grade fabrics can be processed into high-grade coating products. Greatly increase the added value of products.
The pretreatment of coated base cloth is no different from that of other dyeing and finishing processes, but the requirements for the cloth surface are slightly higher, such as complete singeing, smooth and clean cloth surface, without neps, weft skew, and loose edges. For the dye varieties, pay attention to the performance of the dye varieties to prevent the coating products from discoloring too much due to the effect of the solvent in the coating agent and the dye.
Prevent excessive discoloration of coating products due to the interaction of solvent and dye in the coating agent.
4.2 Finishing process of waterproof and moisture permeable coating
There are two ways to finish waterproof and moisture permeable coating: wet coating or dry direct coating.
4.2.1 Wet coating
Wet coating is also called solidification coating. Generally, DMF solvent-based coating agent is used to coat the base cloth, and then it is immersed in the water coagulation bath to extract solvent (DMF), so that the coating film forms micropores and has moisture permeability.
technological process:
Base cloth - pretreatment (dyeing) - shaping - PU coating - solidification (extraction solvent) - washing - drying - finishing - finished product. The water permeability of wet coating products can generally reach more than 100mmH20, and the moisture permeability can reach 3000g/(m2d). The process and auxiliary materials of this method are relatively mature, but the process is cumbersome, solvent recovery is troublesome, adhesion fastness and film strength are not high, and the processing cost is high.
4.2.2 Dry direct coating
Dry direct coating equipment and process are simple, easy to operate and low processing cost. The key of this kind of coating is the coating agent. The performance of the coating agent will determine the waterproof and moisture permeability of the coating product, as well as the performance of the feel, elasticity, film strength, etc.
technological process:
(1) Single-dose coating agent: base cloth - pretreatment (dyeing) - definite form - direct coating - drying - baking - finishing - finished product.
(2) Double-dose coating agent: base cloth - pretreatment (dyeing) - fixed form - primer - drying - top coating - drying - baking - finishing - finished product.
epilogue
PU waterproof and moisture permeable coating products have good elasticity, high strength, low temperature resistance (below - 30 ℃), wear resistance, soft feel, refreshing, certain hydrophilicity, good waterproof and moisture permeable effect, and good application prospects. The waterproof and moisture permeable coating agent for dry direct coating has high technical content. It marks the advanced level of coating processing, which requires simple equipment and simple process, and is the development direction of waterproof and moisture permeable products in the future. At present, there is a large gap between the research and production of waterproof and moisture permeable coating agent in China and foreign advanced level, and the high moisture permeable commercial water pressure coating agent for dry direct coating is still mainly imported. Therefore, accelerating the research and development of high moisture permeable and high water pressure coating agent and its application process has far-reaching significance.
Recommended News