New textile chemicals for improving the color fastness of synthetic fibers
Published Time:
2022-12-18
Since the mid-1980s, the proportion of synthetic fibers in textile fibers in the world has been increasing. Since 1995, the proportion of synthetic fiber has exceeded that of natural fiber and has become the main source of fiber used in textiles and clothing. From the perspective of production tonnage, although the output of raw cotton increased from 17.99 million tons in 1992 to 19.198 million tons in 2002
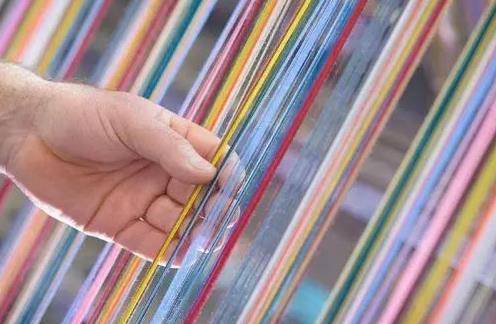
Since the mid-1980s, the proportion of synthetic fibers in textile fibers in the world has been increasing. Since 1995, the proportion of synthetic fiber has exceeded that of natural fiber and has become the main source of fiber used in textiles and clothing. From the perspective of production tonnage, although the output of raw cotton increased from 17.99 million tons in 1992 to 19.198 million tons in 2002, because the output of raw wool decreased from 1.719 million tons to 1.271 million tons in the same period, the proportion of the two in textile fiber decreased by 11% compared with 1992 in 2002, while the output of synthetic fiber filament yarn and staple fiber increased significantly by 1.41 times and 0.56 times in the same 10 years, In particular, the development of synthetic filament yarn provides textile designers and manufacturers with more opportunities to develop new fabrics with innovative aesthetic vision and performance, making its output increase more than 1.5 times of synthetic staple fiber.
Since the mid-1980s, the proportion of synthetic fibers in textile fibers in the world has been increasing. Since 1995, the proportion of synthetic fiber has exceeded that of natural fiber and has become the main source of fiber used in textiles and clothing. From the perspective of production tonnage, although the output of raw cotton increased from 17.99 million tons in 1992 to 19.198 million tons in 2002, because the output of raw wool decreased from 1.719 million tons to 1.271 million tons in the same period, the proportion of the two in textile fiber decreased by 11% compared with 1992 in 2002, while the output of synthetic fiber filament yarn and staple fiber increased significantly by 1.41 times and 0.56 times in the same 10 years, In particular, the development of synthetic filament yarn provides textile designers and manufacturers with more opportunities to develop new fabrics with innovative aesthetic vision and performance, making its output increase more than 1.5 times of synthetic staple fiber. Among the synthetic fibers used in textiles and clothing, polyethylene terephthalate polyester fiber has the fastest growth. The output increased by 14.292 million tons in the 10 years from 1992 to 2002, making its proportion of synthetic fibers in 2002 reach 76%, up 14% from 1992. During the same period, the production of polyamide fiber and polyacrylonitrile fiber increased by 741000 tons and 763000 tons, but their proportion in synthetic fiber in 2002 decreased by 9% and 5% respectively compared with 1992, of which polyamide fiber accounted for 14% and polyacrylonitrile fiber accounted for only 10%. The rapid growth of polyester fiber production capacity and output has led dye manufacturers to focus on the development of disperse dyes for polyester fiber, which is similar to the situation that dye manufacturers focus on the development of reactive dyes for cotton and other cellulose fibers in the field of cellulose fiber dyes. At the same time, the development of blended fabrics composed of elastic fiber (i.e. block polyurethane fiber) and polyester fiber, polyamide fiber, cotton and other cellulose fibers has prompted dyemakers and dyers to make efforts to solve the requirements of dyeing performance and color fastness of these new blended fabrics. In addition, the dyeing performance and color fastness of existing disperse dyes can not meet the requirements of new polyester fibers such as PLA and PIT. All these have promoted the research and development of new textile chemicals to improve the color fastness of synthetic fibers.
A new disperse dye for improving the color fastness of polyester fiber
First of all, the development of ultra-fine polyester fiber, especially the sea-island ultra-fine polyester fiber manufactured by composite spinning method, has greatly improved the wearability of fabrics made of polyester fiber. The textile suede fabric made of it is very similar to natural suede, so the output of ultra-fine polyester fiber has increased year by year. However, the supermolecular and morphological structure of this fiber have changed greatly, and the specific surface area is large, which causes new problems in the use of traditional disperse dyes and early disperse dyes for ultra-fine polyester fiber, such as the dyeing speed, dye uptake, color rendering, levelness and fastness. Therefore, it is urgent to improve and improve the upgrading and fastness of disperse dyes used for ultra-fine polyester fiber. The Lumacron MFB dye developed by M. Dohmen Company is a new generation of disperse dyes. Their structure is designed to meet the high fastness standards required by ultra-fine polyester fibers. They not only have a full spectrum including yellow, orange, bright red, red, ruby, turquoise, blue, navy and black, but also have excellent upgrading, compatibility and wet fastness. The excellent performance of Lumacron MFB dyes makes them have wide adaptability to ultra-fine polyester fibers. Appropriate dyeing auxiliaries such as 1-2g/L, Dispertan MF and 2g/LDoregal WMB are used to match with the dyeing process. They can be used for the dyeing of various ultra-fine polyester fibers such as island type and differential composite type. In order to avoid the two-sided heterochromatic effect, the company recommends the use of three primary colors of Lumicron Orange MFB, LumicronRubineMFB, LumicronBlueMFB or LumicronNavyMFB, which have excellent coverage for the difference in dyeing properties of fibers. M · Dohmen Company recommends DorospersK dye for light color dyeing requiring high light fastness. In addition, the Kayalon Microester dye of Japan Chemical Pharmaceutical Co., Ltd. is also a new type of disperse dye that improves the color fastness of disperse dyes used for ultra-fine polyester fiber in the past. It has four series A, B, C and D, which are suitable for different application requirements. It has good covering property, excellent light fastness, wet fastness and sublimation fastness, and is easy to dye into dark color, It can also be applied to the dyeing of sea-island superfine polyester fiber and differential composite superfine polyester fiber; There are also DianixSF dyes, DianixSPH and UPH dyes from Dystar, which are especially suitable for situations requiring fast diffusion rate.
In recent years, polyester fiber fabrics, such as sportswear, leisure wear, and automobile interior fabrics, need heat setting treatment to ensure the size consistency and stability of the finished products after dyeing with disperse dyes. Due to the high heat setting temperature, which is more than 140 ℃, the disperse dyes in the fiber will have the reverse heat transfer with the dyeing process, and some of the dyes will migrate to the fiber surface again, resulting in the color fastness of the dyed fabric after heat setting, such as washing fastness, perspiration fastness, etc., and will be stained on the adjacent lining or pollute the environment, In the past, the washing fastness of disperse dyes provided by disperse dye manufacturers were all the data of polyester fabrics dyed with disperse dyes, which were reduced and cleaned without heat setting treatment, so they could not reflect the heat transfer performance of disperse dyes. In addition, polyester fabrics after dyeing, reduction and cleaning, especially the blended fabrics composed of polyester fibers and cellulose fibers, often need to undergo soft, waterproof and other finishing. Many softening agents and waterproof agents, such as amino silicone oil softener, are emulsified by emulsifiers made of non-ionic surfactants, which seem to contain soluble disperse dyes, This makes the dyed disperse dyes not only migrate under heat, but also migrate to the fiber surface due to dissolution in the carrier, thus reducing the washing fastness. This migration will occur and contaminate the adjacent white fabric even during storage and transportation. Practice has proved that quite a few of the old disperse dyes have poor heat resistance and migration, which will make the washing fastness of dyed polyester fabric after heat setting treatment or soft, waterproof and other finishing worse, such as C.I. disperse red 54, C.I. disperse red 60, C.I. disperse red 73, C.I. disperse red 152, C.I. disperse red 153, C.I. disperse red 167, C.I. disperse blue 183 and C.I. disperse purple 93:1 Disperse blue EX-SF300% and disperse black EX-SF300% composed of C.I. Disperse Blue 291:1 and C.I. Disperse Orange 76 are such disperse dyes. It should be pointed out that the effect of dyeing polyester fabric on washing fastness after softening and waterproof finishing is related to the properties of softener and waterproof agent, and also to the structure of disperse dyes used for dyeing. For example, polyester fabric dyed with 40g/L disperse dark blue H-GL will reduce washing fastness and fail to meet the requirements when using methylorganosilicon softener for finishing, If fatty amide softener is selected for finishing, the washing fastness can be improved and the requirements can be met; When fluoroacrylate waterproof agent is selected for the waterproof finishing of dyed polyester fabric, the washing fastness will be reduced and the requirements cannot be met. If fluorosilicone waterproof agent is selected for the waterproof finishing, the washing fastness will be improved and the requirements can be met. In order to improve the heat resistance and migration of disperse dyes, Ciba Refinery has successively developed TerasilW disperse dyes and TerasilWW disperse dyes, especially the latter, which are the third generation washable disperse dyes with phthalimide azo structure, covering the whole color range, and the fabrics dyed with them have excellent washing fastness after heat setting or softening, Even under strict washing conditions (such as washing at 60 ℃), they can still meet high washing requirements. They have greatly improved and improved compared with the first and second generation washable disperse dyes. For example, the first generation of washable disperse dyes, such as C.I. Disperse Red 111 and C.I. Disperse Blue 284, have improved their washability compared with C.I. Disperse Red 167, but have poor fastness to strict washing tests, washing of blended fabrics composed of polyester fibers and other fibers, and washing of dark fabrics; The second generation washable disperse dyes developed since then, such as C.I. Disperse Red 356, have excellent washing fastness (even under very severe conditions), but their dyeing performance is not satisfactory, especially the reproducibility of the upgrading property is poor, the sensitivity to dyeing conditions such as dyeing temperature is high, and it is difficult to dye dark. The third generation washable disperse dyes not only improve the washing fastness of the second generation dyes, but also improve other dyeing properties, as shown in Table 1:
Lumicron MFB dyes also exhibit excellent heat resistance and migration. For example, the contrast test at 60 ℃ for 5 weeks shows that they have little stain on white polyester fibers. Even if Lumicron Black MFB is used for dyeing, the dyed fabrics are also stored after softening and finishing. Dystar's DianixXF and DianixSF dyes are also new dyes with excellent washing fastness, such as DianixBfill.ScarletXF, and DianixRedSE-3B, DianixRoyalBlueSE-R and DianixYellowSE-GBN, which constitute tri-color disperse dyes with high heat resistance, high washing fastness, high strength and high upgrading, The polyester fabric dyed with it not only has excellent washing fastness after heat setting treatment or soft finishing, but also can be used to replace the low-energy and medium-energy tricolor disperse dyes composed of disperse red 3B, disperse blue 2BLN and disperse yellow RGFL (disperse yellow RGFL is a prohibited dye).
With the continuous improvement of the requirements for the dyeing fastness of automotive interior decorative fabrics, Dystar has developed a series of new high-light fastness disperse dyes to replace the old disperse dyes, such as the DianixHLA series dyes, which not only have higher light fastness than the Dianix KIS-U dye (for light color) and the Dianix KIS-M dye (for medium color), but also can solve the problem of color uniformity in the surface and inside of the fabric when dyeing with Disperse Black SPC; Dianix AM Specialties dyes have higher light fastness than Dianix AM Classics dyes, and are suitable for dyeing from light to dark, while Dianix AM-SLR dyes are a kind of disperse dyes with ultra-light fastness, and are also suitable for dyeing from light to dark in a wide range. The Dianix AM Formula One dyes developed on the basis of this not only have ultra-light fastness and no color change at high temperature, Moreover, it is fully compatible with the new daylight test requirements formulated by General Motors of the United States and the light fastness requirements and other tests stipulated by the International Association of Automobile Manufacturers. They have four main varieties and five auxiliary varieties, which can cover more than 90% of the common colors.
2 New dyes and auxiliaries for improving the color fastness of polyamide fiber
In recent years, the application of polyamide (nylon) filament yarn in sportswear and clothing made of its blended fabric with elastic fiber has grown rapidly. In order to make the dyed polyamide fiber have better color fastness, Dystar Company developed IsolanNHF-type dyes, which are 1:2 metal complex dyes with overall fastness and are used for polyamide fiber dyeing, not only have super light fastness and high wet fastness, Moreover, it has excellent compatibility and good homochromaticity of polyurethane elastic fiber, greatly improving the color fastness of previous dyes, and can cooperate with TelonM type dyes (acid dyes) and IsolanS type dyes (metal complex dyes) at will. M. Dohmen's Dorasyn XL type dyes introduced to the market are also a kind of modified acid dyes that improve the color fastness of polyamide fibers used in the past. They have excellent wet fastness and excellent levelness, which is the characteristic of this type of dyes different from other dyes, because other dyes used for dyeing polyamide fibers often have to choose between color fastness and levelness; In addition, this kind of dye does not contain metal (except turquoise blue dye), which has greater ecological safety; In order to make good use of such dyes and ensure good dye uptake and high color fastness and reproducibility, M. Dohmen recommends Doregal XL as a suitable leveler instead of the common leveler supplied on the market; If the polyamide fabric shows obvious weft stripes, it is necessary to add 2.5% - 5.0% DoregalBRC. If necessary, you can use Dompal B conc (a non-volatile acid) in order to obtain better dye uptake and fixation rate, the initial pH value of the dye bath can be adjusted to 3.5 with DonapalBconc. when dyeing dark colors, and the final pH value can also be adjusted to 3.5 as needed; For polyamide fabrics with higher requirements for color fastness, such as high-standard alkali perspiration fastness, washing fastness and chlorine water fastness, they can be treated with a treatment bath containing 3% - 4% DomfixACL at pH4.5 and 75 ℃ for 10-20 minutes after dyeing.
In addition, white synthetic fabric such as polyamide fabric has a yellowing problem during storage or transportation. This phenomenon often occurs at the place where the fabric or clothing contacts with the packaging material. That is because the packaging material contains a colorless additive, namely butylated hydroxybenzene (BHT), which is an antioxidant and will be transferred to the textile when it contacts with the textile, It reacts with nitrogen oxides (NOX) from the exhaust smoke on the textile to produce a yellow nitro dye, whose production rate increases with the increase of ambient humidity and temperature during transportation or storage. In response to this problem, BASF has successfully developed a new auxiliary agent TX1567, which can be reliable
Recommended News