Pay attention to those problems when selecting additives
Published Time:
2022-07-13
The following problems must be paid attention to when selecting auxiliaries to help improve the quality of finished printing and dyeing products
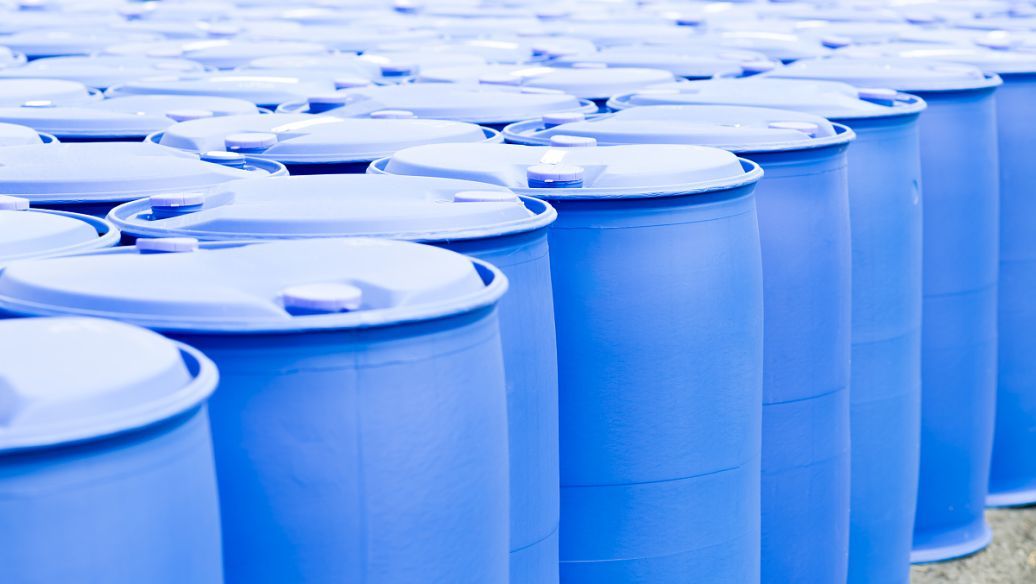
The following problems must be paid attention to when selecting auxiliaries to help improve the quality of finished printing and dyeing products
1. Technicians must master the basic knowledge of additives
This is the premise of selecting additives. In order to make good use of additives, we must have a basic understanding of the basic concept, basic structure, performance and use characteristics of additives. If any abnormality is found, we can also analyze the cause and deal with it in time. For this reason, an overview section is written at the front of each chapter in my manual, describing the action principle, basic characteristics, structure classification, use method, application detection method and points of attention when using this kind of auxiliary agent, so that the reader can basically master the knowledge of this kind of auxiliary agent and lay a foundation for correct use. In the introduction of each auxiliary agent, its basic structure, properties (ex-factory standard), use and use method are introduced one by one. If the structure type is the same, Its use method and performance are also roughly the same, which can be doubled by one. If you know the basic structure of the varieties not collected in the manual, you can also know them at your fingertips. Therefore, when using new additives, each factory must inform the supplier of the structure category of the additives. For example, the application factory should know which type of softener belongs to amino silicone oil softener, hydroxyl silicone oil softener, fatty amide softener, imidazoline softener, and fatty acid paraffin softener. Only in this way can we master its basic performance and prevent blind use.
2. Have a basic understanding of the solubility of additives and the stability of hard water and metal ions
For example, the solubility of anionic surfactants in alkaline solution is greater than that in acid solution, while the solubility of cationic surfactants is the opposite. Amphoteric surface solid surfactants have the characteristics of both anions and cations, while non-ionic surfactants have less influence. The solubility of the first three surfactants increases when the temperature rises, while the solubility of non-ionic surfactants decreases with the temperature rising, so there is a cloud point. The cloud point must be higher than the use temperature, otherwise it will lose its efficiency and play no role as an assistant. The cloud point increases with the increase of EO number. It increases with the amount of anionic additives. However, it decreases with the increase of electrolyte content. If Pingpingjia is used as a leveling agent or dispersant for high temperature and high pressure dyeing, it will fold out in the dye solution because the temperature of use is much higher than its cloud point (generally about 75 ℃). It will not work, but will condense the dye and cause color spots. Organosilicon defoamer is a lotion of methyl silicone oil or ethyl silicone oil emulsified with non-ionic surfactant and white carbon black. If the emulsifier with low cloud point is used, the same problem will occur. The auxiliary factory often does not pay attention to this problem, which will cause great harm to the printing and dyeing factory. See our manual 5-013 for the example method of cloud point, and 6-035 for the determination method of surfactant solubility.
3. The acid and alkali resistance of additives must be determined:
This is easy to understand whether the auxiliary agent can meet the needs of the process. The acid-resistance and alkali-resistance of auxiliaries vary greatly. Anionic surfactants are generally alkali-resistant but not acid-resistant. Phosphates have the best alkali-resistance, while carboxylic acids have the worst acid-resistance. Cationic surfactants are generally acid and alkali resistant. Non-ionic surfactants can resist weak alkali and weak acid, but not strong acid and strong alkali. The printing and dyeing factory must first test whether the auxiliaries used will be turbid or precipitated when they are used according to the process requirements. One factory uses imported auxiliaries to conduct underwater track scouring and bleaching. At first, no problems are found, and then there are wrinkles. There are also irregular color spots scattered on the cloth surface after dyeing. Open the box to see that the guide rollers are bound with solid substances of different thickness, which are originally precipitated due to the alkali-resistance of the auxiliaries. When they are adhered to the cloth, color spots will be formed during dyeing. Therefore, the alkali and acid resistance of additives must be determined. This should be paid more attention to during cold pad-batch scouring and bleaching. Many additives will hydrolyze in alkaline and acidic media. See manual 6-017 and 6-018 for the determination method.
4. The ionic property of additives must be mastered
There are four kinds of additives: anions, cations, nonions, and amphoteric. The first three are commonly used. Anions cannot be used in the same bath with cationic additives. When they are together, they will form flocculent precipitation, which will not only play a role, but also form dyeing defects. This ion can be used in the same bath with cationic or anionic additives. These principles are well known, but they are often unconsciously ignored in actual production. For example, the fixing agent is cationic and cannot meet with anionic auxiliaries. However, many factories use anionic soap detergent to wash after direct, acid and reactive dyes are dyed, but then they do not wash the detergent, and then they fix the color with the fixing agent. At this time, the fixing agent is integrated with the washing agent on the cloth, which not only wastes the fixing agent to reduce its fixing effect, The soaping and rubbing fastness of dyes are also affected by the precipitates of soaping and fixing agents.
5. Do not reduce the amount of additives at will:
The components of printing and dyeing auxiliaries can be roughly divided into two categories, namely, the auxiliaries of the complex of functional auxiliaries and surfactants. The former uses different compounds to play a functional role in processing, such as oxygen bleaching stabilizer, color fixing agent, color modifier, defoamer, softener, green agent, water repellent, oil repellent finishing agent, flame retardant, anti-wrinkle finishing agent, and so on. They can achieve the desired effect only at a certain amount. The other is that surfactants are used as printing and dyeing auxiliaries, such as penetrants, detergents, levelers, scouring agents, silk foaming agents, dispersants, emulsifiers, etc. Their effect is actually to play the role of wetting, emulsifying, dispersing, solubilizing and other functions of surfactants, which is the specific performance of their comprehensive effects or single effects. Therefore, they fully conform to the theory of surfactants, and therefore, we should learn the knowledge of surfactants. Surfactants will form micelles in the process of dissolution, and the concentration of micelles is called critical micelle concentration, or c.m.c. The number of micelles with a concentration of more than c.m.c increases, and the micelles become larger. The wetting action of surfactants can occur below the concentration of c.m.c. The emulsification, solubilization, dispersion, and cleaning actions are all micelles, so they must be above c.m.c to have an effect. Generally, the c.m.c value of pure surfactants is not more than 0.2g/L, while the amount of surfactants in most products is only 15-20%. With other auxiliary materials, the total solid content is 40%. Therefore, the c.m.c value of products is not more than 1g/L. In other words, the concentration of additives used must be at least 0.5g/L before micelles are produced. When the concentration is greater than this, the micelle amount increases, and the effect is significant. Therefore, the amount of additives cannot be reduced at will, Especially for the cheap detergent sold in the market, its effective ingredient is only 5%, a large amount of which is sodium sulfate, etc., and it can not achieve the washing effect if it is used less. This is the reason why the dosage of soap is set at 3g/L when the national standard and ISO standard do the soaping fastness test. Wetting penetration is not the function of micelles but the function of monomolecular surfactants, so it can be below c.m.c, and the concentration in the processing fluid need not exceed 1g/L.
6. Additives must be dissolved and diluted before being added to the processing fluid:
Due to the different specific gravity and solubility of raw materials, the mixed additives often form different upper and lower layers in the commercial additive solution, which affects the effect. After a long storage time or in cold weather, turbidity or even stratification may be formed due to solubility changes. This phenomenon is allowed as long as it is not lotion. However, when weighing materials before use, the operator must be strictly required to mix evenly before weighing materials, In case of lotion, turbidity and stratification are not allowed. This means that the lotion has been demulsified and cannot be used again, or it must be emulsified after rapid mixing. It can only be used when it is proved to be usable by high-speed centrifugal separation test, and it must not be used by manual mixing.
The solid additives must be dissolved in hot water and used thoroughly. The liquid additives must be diluted with warm water before use. The additives with high viscosity must be gradually diluted with water after mixing. The additives that are easy to mildew, such as fat softener and slurry, can be removed from the upper layer as long as they are not diluted and there are not many mildew spots. The additives below can also be used. If they become thinner, they can be returned.
The dissolved and diluted auxiliaries are added to the treatment bath according to the process requirements. Generally, they are added to the treatment solution before the fabric enters the treatment bath, and then introduced into the fabric after the solution is circulated to make it uniform. If it is a leveling agent, the fabric is run in the leveling agent for several minutes before adding the dye solution.
Recommended News